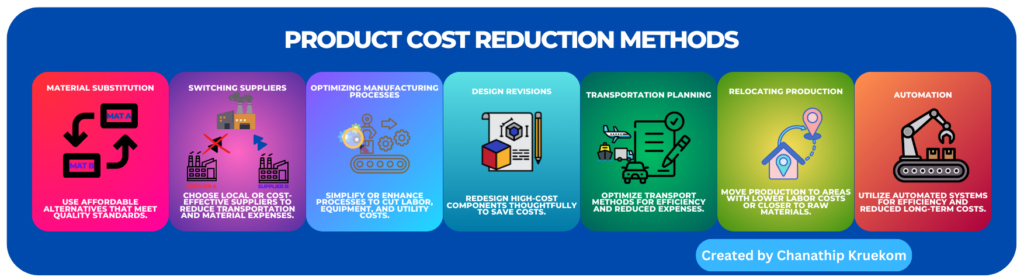
When designing and developing a product, it is critical to choose the right materials, production methods, and processes to ensure that it satisfies the requirements and specifications. All of these decisions, including product design, material selection, structure, and production quantity, influence the product’s cost. Here, I discuss various cost-cutting solutions that I have encountered and applied.
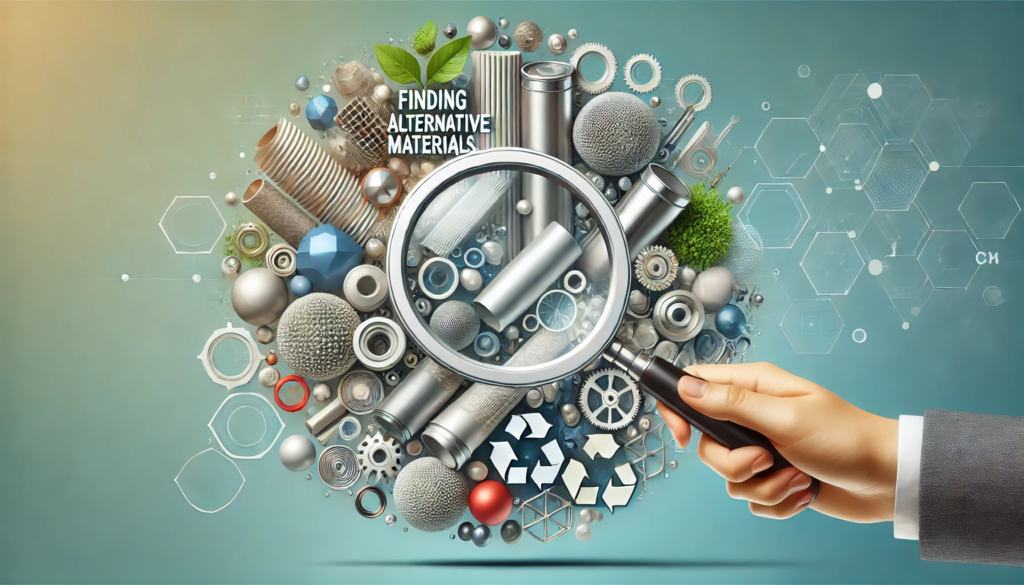
1. Finding Alternative Materials.
A frequent method is to replace existing materials with more cost-effective ones. These substitutes must have capabilities and quality that are comparable to or better than the original materials. They should also go through rigorous testing to ensure that the product and material criteria are met, and that product quality is not affected.
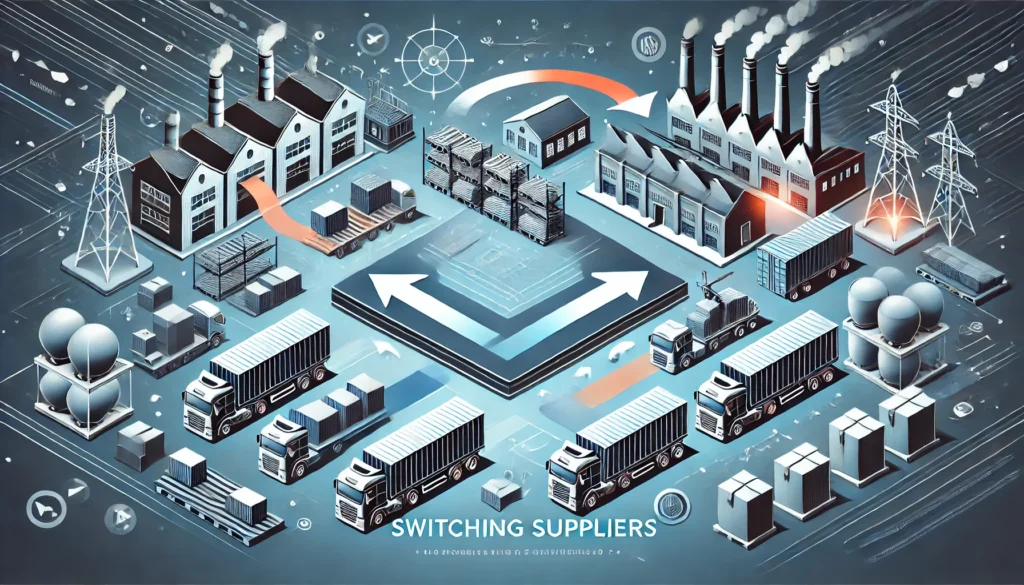
2. Switching Suppliers
By choosing suppliers near the factory, sourcing locally rather than importing, and streamlining transportation, switching suppliers can lower costs—even for the same material. The cost of production can be significantly decreased by these adjustments.
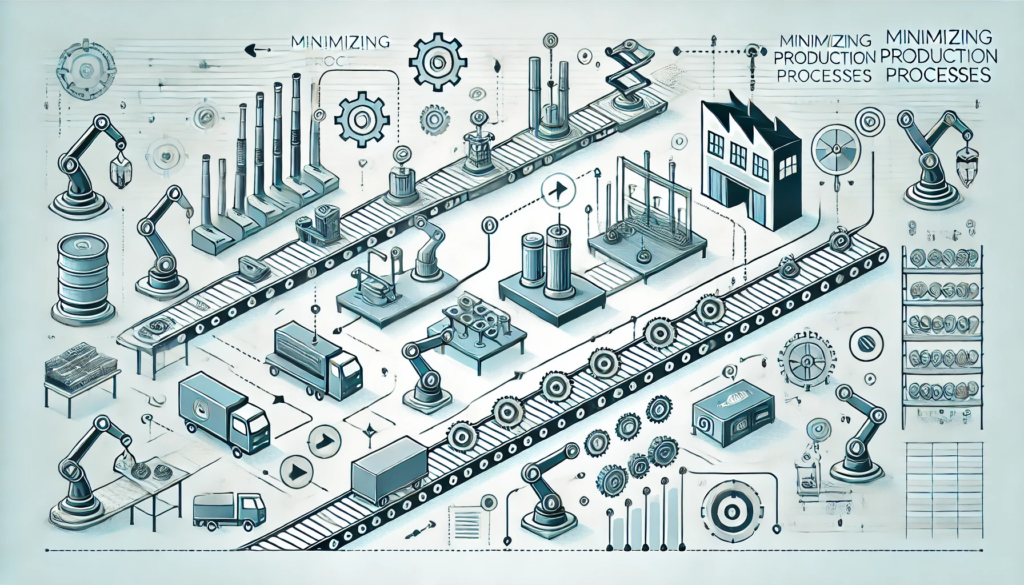
3. Minimizing Production Processes
One of the most expensive production processes is manufacturing. Costs can be considerably decreased by cutting back on or changing these processes. Cutting stages, for example, can save money on labor, equipment, and maintenance while slowing productivity. However, improving procedures can speed up output, which lowers overtime and utility expenses. The particular production requirements determine the most effective course of action.
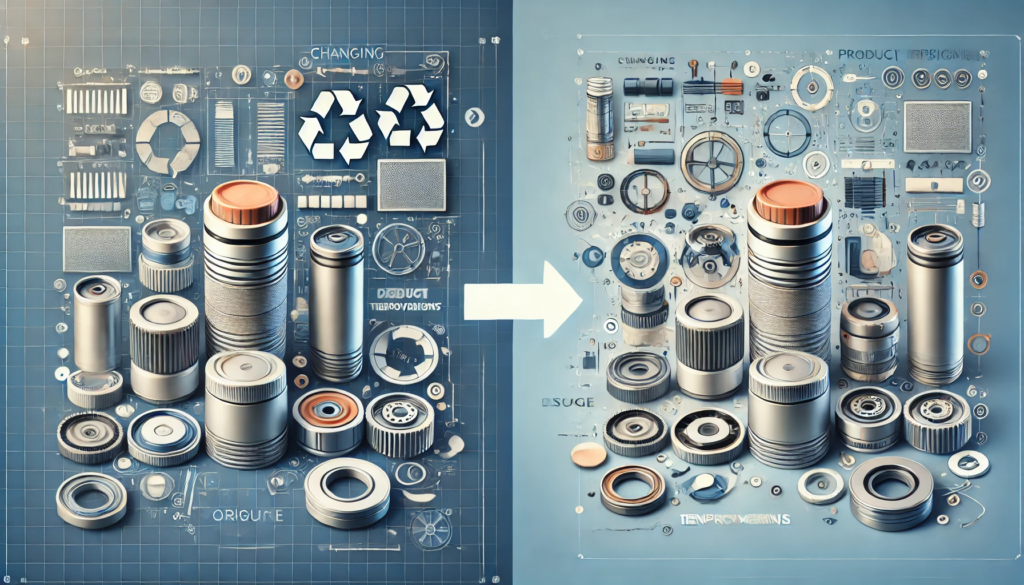
4. Changing Product Designs
Another efficient strategy is to alter product designs in order to cut expenses. However, as design is a core component of production, any modifications must take downstream impacts into account. For example, changing plastic parts often requires costly mold modifications or new molds, thus such changes are only practical for expensive parts.
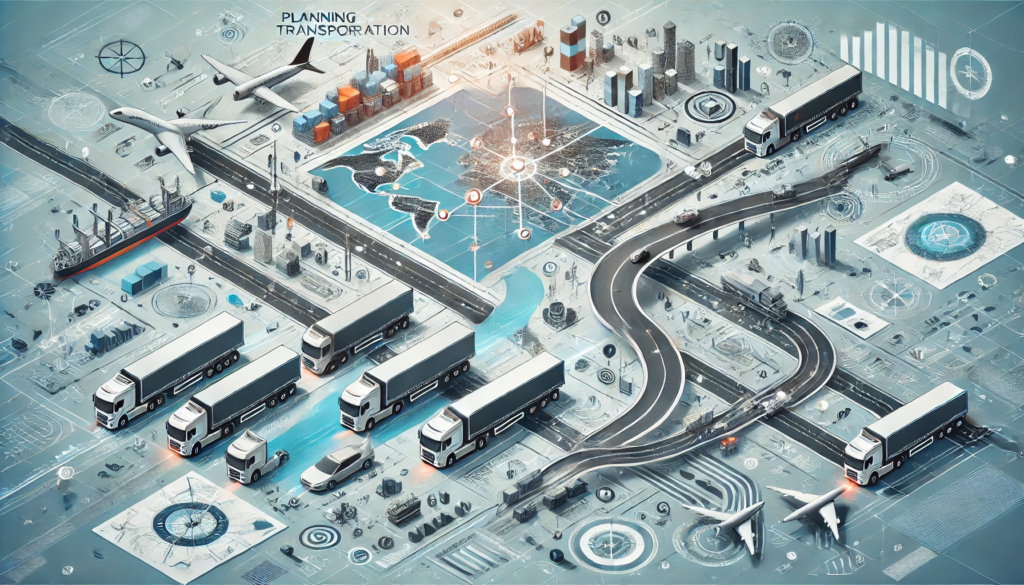
5. Planning for Transportation
One of the biggest expenses in product delivery is transportation. Costs can be significantly decreased by using suitable techniques and efficient planning. Reduced costs are made possible by the wide variety and ease of today’s transportation options.
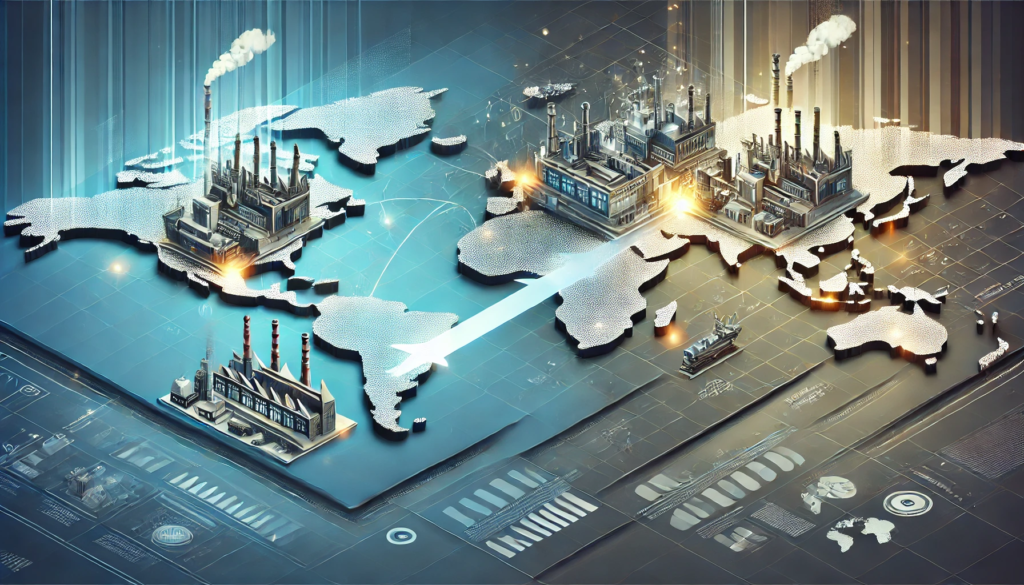
6. Relocating Production Plant
Costs can be significantly reduced by moving production plants to nations with cheaper labor or nearer supplies of raw materials. Additionally, for some components, it may be less expensive to outsource production to vendors rather than produce them inside. To ensure quality, labor skill levels must be taken into consideration as well.
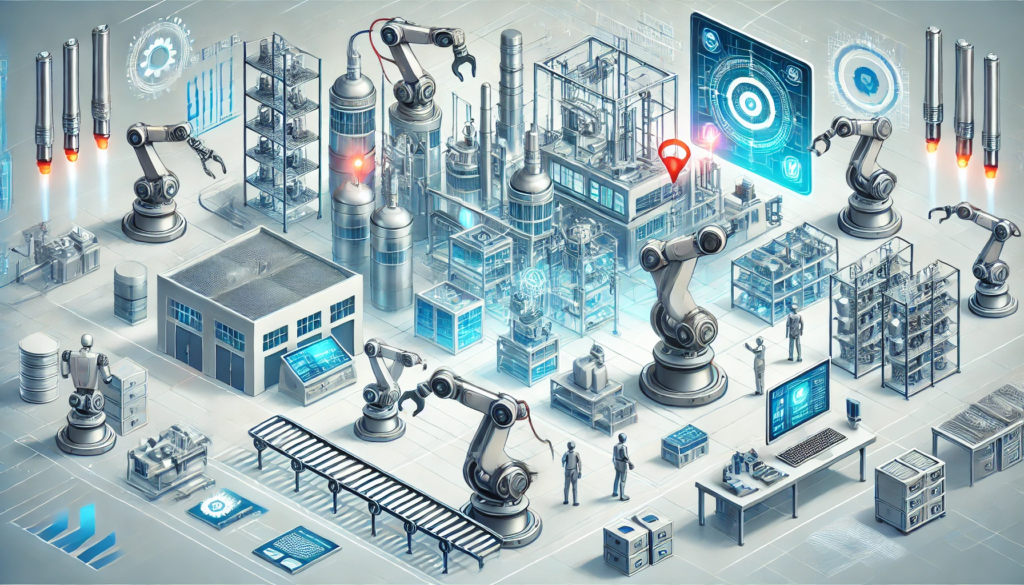
7. Making Use of Automation Systems
Automation eliminates the need for human labor and runs continually. It is perfect for making goods in large quantities using standardized designs and production techniques, greatly increasing productivity and lowering long-term expenses.
In conclusion
Optimizing materials, manufacturing processes, and logistics while preserving quality and maintaining specifications is necessary to lower product development and design costs. Using less expensive substitute materials, moving to nearby or more efficient suppliers, optimizing production processes, and changing designs for expensive parts are all examples of successful tactics. Other strategies include moving production to regions with cheaper labor costs or nearer raw resources, automating production for reliable, high-volume output, and organizing transportation to cut delivery costs. When combined, these techniques greatly reduce expenses and increase efficiency without diminishing quality.