In my experience, selecting the Parting Line (P.L.) for plastic products is usually based on simplicity and logical design. The placement of the Parting Line is crucial because it affects the final appearance of the molded product, the mold design, and possible issues during injection molding.
The Parting Line selection can be considered from two angles:
1. Product designer’s perspective.
2. Mold designer’s perspective.
Both points of view must be aligned and clearly understood, as both sides have distinct responsibilities. After the design process is complete, talks are made to establish the best Parting Line placement. The following are significant considerations for determining the Parting Line based solely on my experience as a product designer.
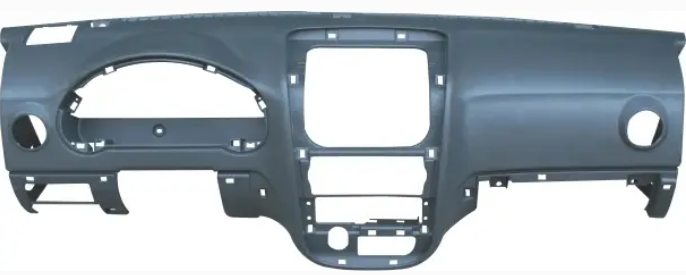
1. Avoid Visible Areas.
The Parting Line should not be applied to visible surfaces or areas that require a beautiful finish. A badly placed P.L. might cause a flash at the contact point of the Core and Cavity molds or Slides, resulting in an unsatisfactory surface finish.
Tip: If positioning the P.L. in such a location is inevitable, a Surface Finish treatment and Surface Coating can be used to conceal flash lines, although this raises production costs.
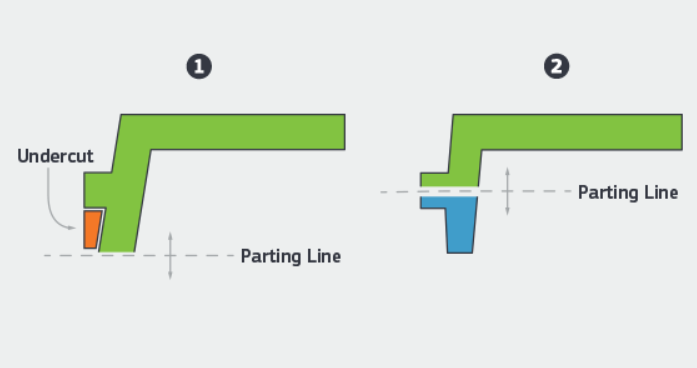
2. Avoid Undercuts.
The Parting Line (P.L.) is normally placed in the simplest and most logical location, whether for low or high-complexity products. However, structural complexity frequently causes common concerns such as undercuts, which might prevent correct mold ejection. As a result, the P.L. should be put at a location that prevents undercuts; otherwise, the mold will not be separated.
Tip: If an undercut is unavoidable and the design cannot be changed, another option is to separate the complexity sections, manufacture it separately, and assemble it afterward. However, this strategy raises production costs.
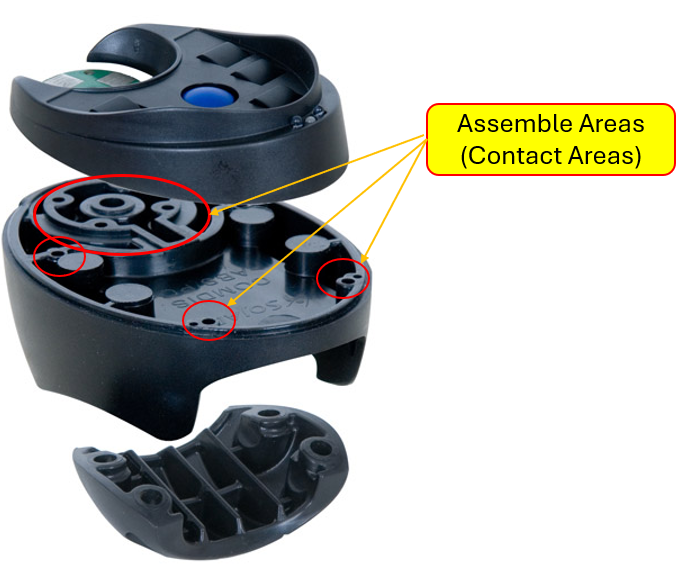
3. Avoid Assembly Areas
The Parting Line (P.L.) should not be placed on or near the assembly points of a component. Assembly areas typically require high precision and low tolerance variation, often controlled by Geometric Dimensioning & Tolerancing (GD&T) to prevent assembly issues. Improper P.L. placement in these areas may lead to misalignment, affecting the product’s functionality. To avoid potential problems during assembly, the P.L. should be positioned away from these critical locations.
Tip: If placing the P.L. in an assembly area is unavoidable, applying a Surface Finish treatment can help minimize assembly issues. However, this increases production costs. Whether adjustments are necessary depends on the product designer’s perspective and the quality assurance standards of the final product.
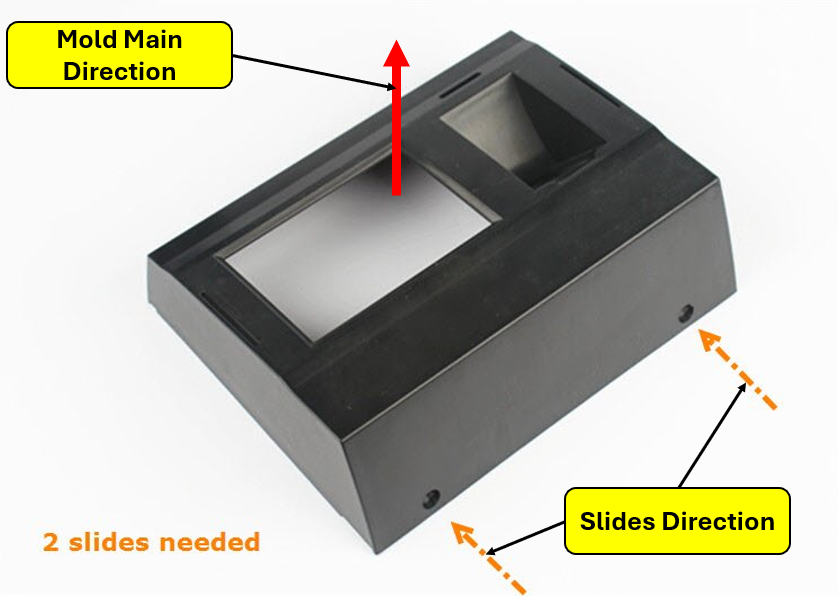
4. Avoid Slide Areas.
For simple parts, slides may not be necessary. Slides are necessary for creating specific details in complex parts where certain structures are not aligned with the main mold axis. In such circumstances, avoid placing the Parting Line (P.L.) in regions where Slides are employed. This is because the Slide axis is not aligned with the main mold axis, which might cause mold ejection issues and probable molding flaws.
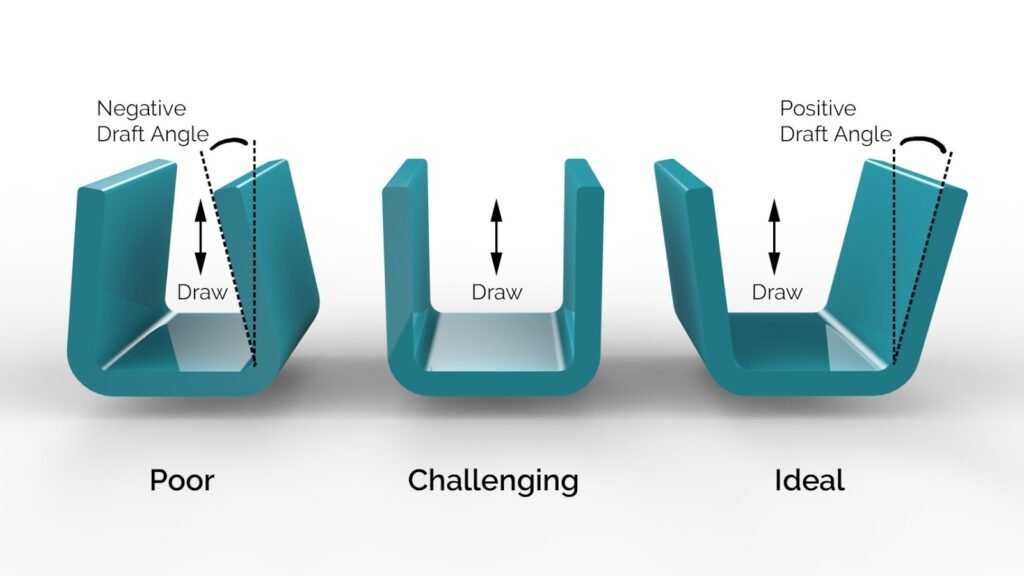
5. Apply the Draft Angle.
If the Parting Line (P.L.) is positioned in an area with significant height or depth, or if the design is likely to make mold injection difficult, a Draft Angle should be used. This allows for easier ejection of the mold following injection molding. However, in other cases, a Draft Angle may not be required for every spot, and the designer should make the final decision.
Tip: The Draft Angle degree is determined by the product size (dimension of the target areas) and the ease of mold release. A large Draft Angle may have a negative impact on the product’s structure. To identify the best angle, speak with both the product designer and the mold designer.
These considerations are based on my personal experience in Parting Line selection for products I have designed. The Parting Line placement process involves various factors that differ depending on the specific product. Effective communication and mutual understanding between the product designer and mold designer are essential to ensure the best results for both sides.